In this article we examine how manufacturing businesses in the Northamptonshire region are adapting their approach to recruitment to meet the challenges currently faced by the sector. It’s a big step from ‘just’ shoe manufacturing.
As one of the UK’s leading centres for the advanced manufacturing sector, Northamptonshire is home to more than 1,000 manufacturing companies – from food production to automotive engineering – employing over 40,000 people. There is some exceptional talent, and a host of innovative, sector-leading businesses in the region, with a growing number of new industrial business parks across the area.
Inevitably, with such a densely populated manufacturing and engineering business landscape, the region also faces the sectors’ recruitment challenges in full force, with difficulties in finding and retaining qualified and skilled manufacturers and engineers.
Recruiting top talent in the manufacturing and engineering sectors has long been difficult, and 2023 brings fresh challenges – with the ongoing impact of advancing technology, such as AI and automation, and the continued battle for younger, entry-level talent as older, more experienced talent is approaching retirement and leaving the industry.
As a result, many manufacturing businesses are concerned about the impact of people risks and skills shortages on their future. However, with naturally innovative talent, the sector now faces a critical opportunity to upskill its existing teams – and invest in the future generation of talent – to capitalise on impressive growth opportunities.
A widening skills gap
One of the main challenges facing manufacturing and engineering businesses in Northamptonshire is the ever-widening skills gap. According to the Office for National Statistics (ONS), the UK manufacturing industry has a high demand for engineers but faces a low supply of graduates entering the field. This issue is magnified by the sector’s ageing workforce – with many businesses flagging this as a key concern for long-term growth.
With the average age of UK’s manufacturing and engineering workers continuing to rise, and many organisations struggling to attract and retain the younger generation of talent, the skills gap is widening, and there’s a long-term recruitment challenge on the horizon for the sectors.
Impact of the cost-of-living crisis
The cost-of-living crisis, in particular fuel costs, is also impacting the talent pool for employers and placing greater pressure on wages.
To compete successfully for both new, existing and specialist talent, businesses need to redress this balance – ensuring financial incentives are keeping pace with the economic landscape. However, businesses also need to consider the full benefits package – beyond financial incentives – to truly stand out and attract top-tier talent in the sectors.
Attracting, retaining and upskilling talent to secure growth opportunities
How are successful manufacturing firms managing to attract new people and grow? There are common themes among the businesses we work with, and it’s not all about salary.
Although salary and financial incentives are clearly important, other, non-financial working benefits are also important to today’s manufacturing and engineering workers – including a four-day working week (30%), flexi time (29%) and private healthcare and health insurance (both 24%).
However, Reed’s research also shows that the reality is many of these benefits lag behind expectations, with only 10% benefitting from a four-day working week, 20% flexi time and 16% private healthcare and health insurance. Concerningly, 24% of people in the sector claim they don’t receive any benefits at all.
This highlights a key opportunity for manufacturing and engineering businesses to review both the salary and rewards packages they’re offering and assess whether these are meeting the needs of both existing and prospective employees in today’s business landscape.
While hybrid working and a four-day working week are wanted by some in the sector, it can be tough as an employer to offer these benefits in an engineering or manufacturing environment due to the physical constraints of many of the processes, but there is still room for employers to be flexible to some degree. By offering flexible start and finish times – perhaps incorporating a rota system, or an annual leave allowance above the industry average, you will certainly attract more people to work for you.
In the current environment, a clearly defined company culture, and a detailed vision for the business is critical when attracting talent. Recently, a local automation manufacturing business secured a production supervisor by being able to articulate their values clearly – this was done throughout the recruitment process from the advert to onboarding. The candidates applying for the role all identified with the organisation’s values which align with theirs, so much so that the professional who accepted the offer did so for the same salary he was earning in his previous role.
Skills development, and embracing new methodologies are also big draws for those looking to work in the sectors. Companies that can lay out what learning and development opportunities are on offer during the first three years of a job routinely attract a higher calibre of candidate.
At Reed, we have extensive experience in managing high-volume manufacturing and engineering contracts across the Northamptonshire region, deploying workers to some of the area’s largest business parks. We also have a range of local recruitment experts across Northamptonshire, Buckinghamshire, Bedfordshire – and throughout the UK – to help you to find the talent you need to grow.
For more information, visit www.reed.com
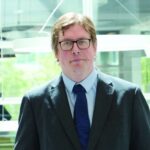